Specialised glass colouring technology
Giving depth of colour, vibrancy & versatility
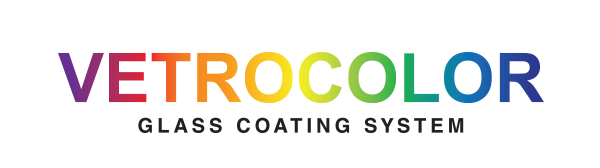
Vetrocolor combines a unique priming system with a specialised colouring technique.
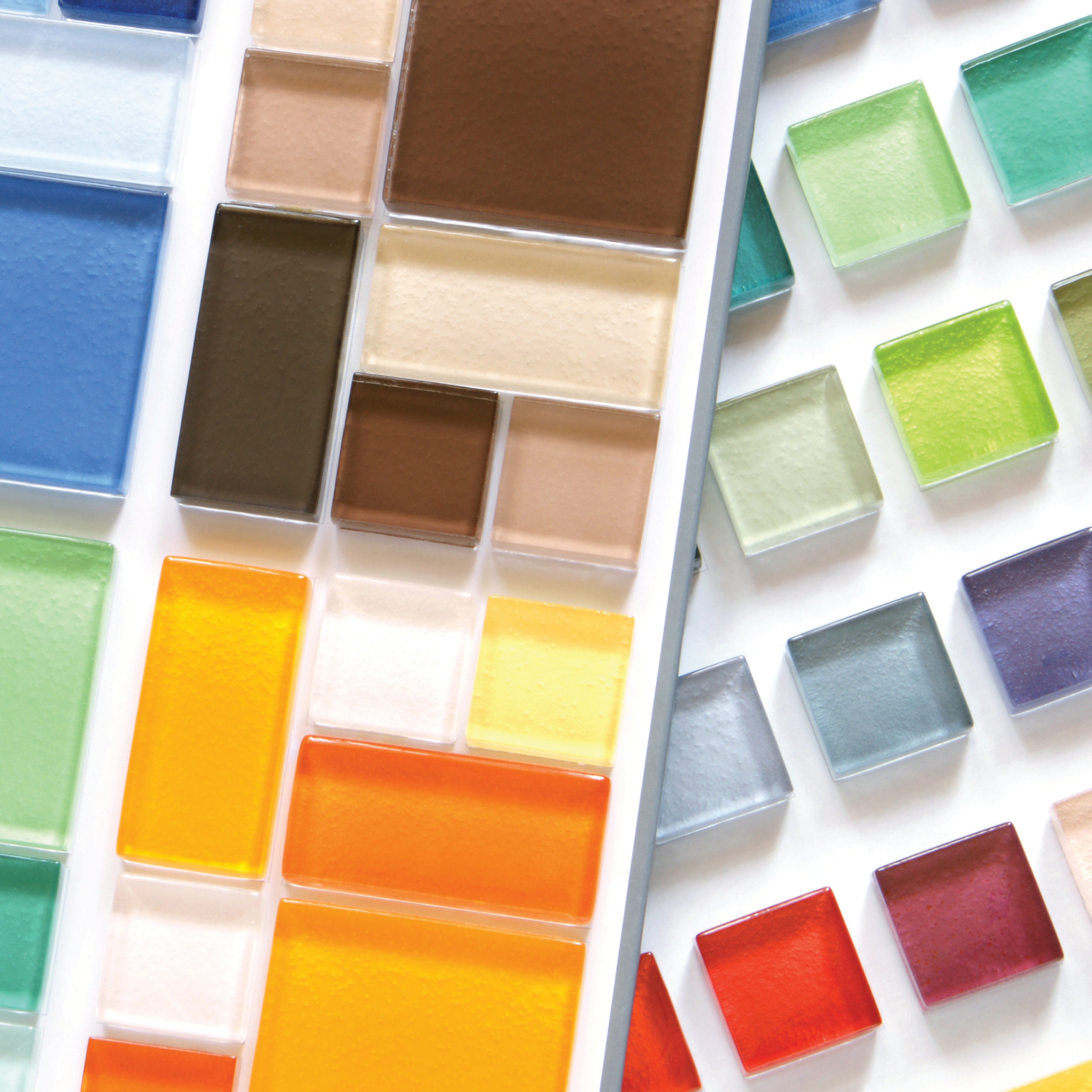
Developed by BC Coatings, Vetrocolor combines a unique priming system with a specialised colouring technique to permanently bond coatings to glass surfaces, giving depth of colour, vibrancy and versatility.
A Vetrocolor coating applied to tempered glass provides the strength and durability to suit almost any architectural application. BC Coatings has a long and established reputation for quality and service, especially in the realm of glass coatings.
BC Coatings have been actively involved in the manufacture and the application of specialised coatings for the glass industry for over 35 years.
A system was initially developed for the adhesion of decorative
coatings on bottles (perfume, essential oils and wine).
This system of glass decoration has been modified and has evolved into the Vetrocolor Glass Coating System. The system can be utilised to decorate toughened, annealed, bent, laminated and textured glass. The range of finishes include, Opaques, Metallics, Pearlescent and Multi-coloured finishes. The Vetrocolor System has been marketed to architects and designers in recent years. Its ability to offer specifiers an unlimited spectrum of colour options quickly and effectively has led to an enormous increase in the specification of decorative glass.
As well as the Vetrocolor Glass Coating System which is applied through a spray gun system, BC Coatings are now actively involved in transferring existing glass technologies to be utilised in the screenprinting on glass and tinted/coloured laminated resins.
Adhesion.
Manufactured under exacting conditions, Vetrocolor is guaranteed to offer permanent bonding between the coating and the glass surface.
The urethane is incorporated into a system which includes associated primers and cleaners. Extensive testing has proven conclusively, Vetrocolor’s superior durability and outstanding performance on a production scale.
Vetrocolour displays excellent adhesion and resistance to chemicals and heat, maintaining colour depth, vibrancy and structural integrity.
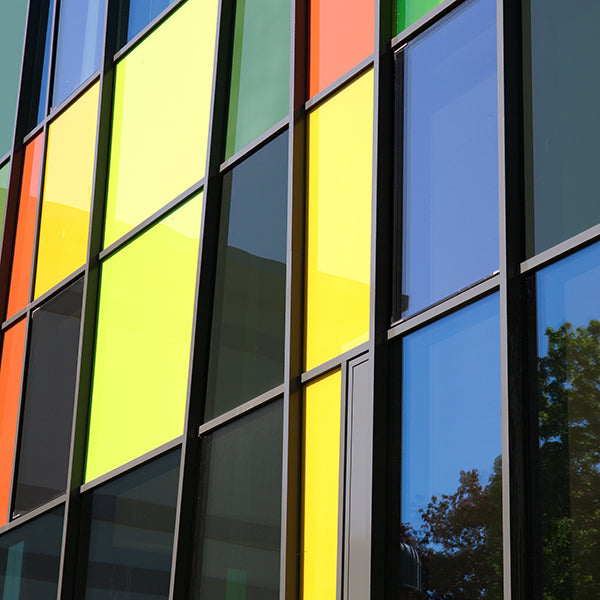
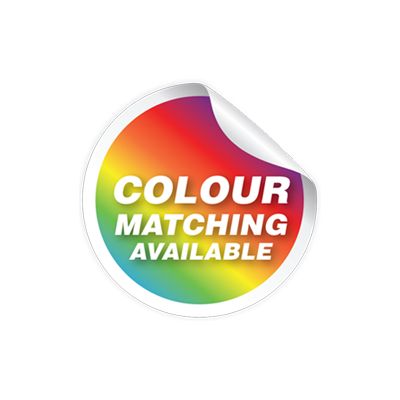
Colours.
The tinters we offer are:
7023 White
7500 Black
Clear
Hi-op White
0925 Red
1010 Bright Red
1102 Maroon
1980 Violet
2616 G/S Blue
2730 Blue
3300 Green
4026 Primrose
4095 Med. Yellow
4621 Yellow Oxide
5870 Scarlet
6219 Red Oxide
As well as the 16 colours available off the shelf in 1 & 4 Litre sizes, we also offer a colour matching service to our customers in any size required.
Vetrocolor Products.
- 8100 Clear
- 7016 White
- Hi-op White
- 7500 Black
- 0925 Red
- 1010 L/F Bright Red
- 5870 L/F Scarlet
- 1102 Maroon
- 6219 Red Oxide
- 1980 Violet
- 2614 GS Blue
- 2730 Blue
- 3300 Green
- 4026 L/F Primrose
- 4095 L/F Med Yellow
- 4621 Yellow Oxide
- 4636 Transparent Yellow
- 9163 Fine Pearl
- 9153 Medium Pearl
- 183 Coarse Pearl
- 8367 Fine Sparkle Silver
- 8357 Medium Sparkle Silver
- 8362 Coarse Sparkle Silver
Requirements.
The Vetrocolor Glass Coating System is a relatively cost effective means of manufacturing a high quality product under controlled conditions. The following equipment and facilities are required for minimum start-up. Equipment requirements can be scaled according to expected production levels.
Spray Booth |
Fully enclosed or open. Size dependent on production requirements. |
Compressor |
A clean air system and moisture / oil regulator. The capacity of the regulator is related to expected volume and output. |
Scales |
Electronic scales with a tolerance of 0.1 grams. |
Batching Oven |
A heating or baking oven will help facilitate cure times and increase production. |
Factory space |
A minimum of 200 sqm will be sufficient to start producing panels. |
Racking |
Panels need to be separated for curing. |
Spray Gun |
Coating applied using standard spray guns. |
Spray Masks |
Approved spray masks to be used as per 2 pack polyurethane guidelines. |
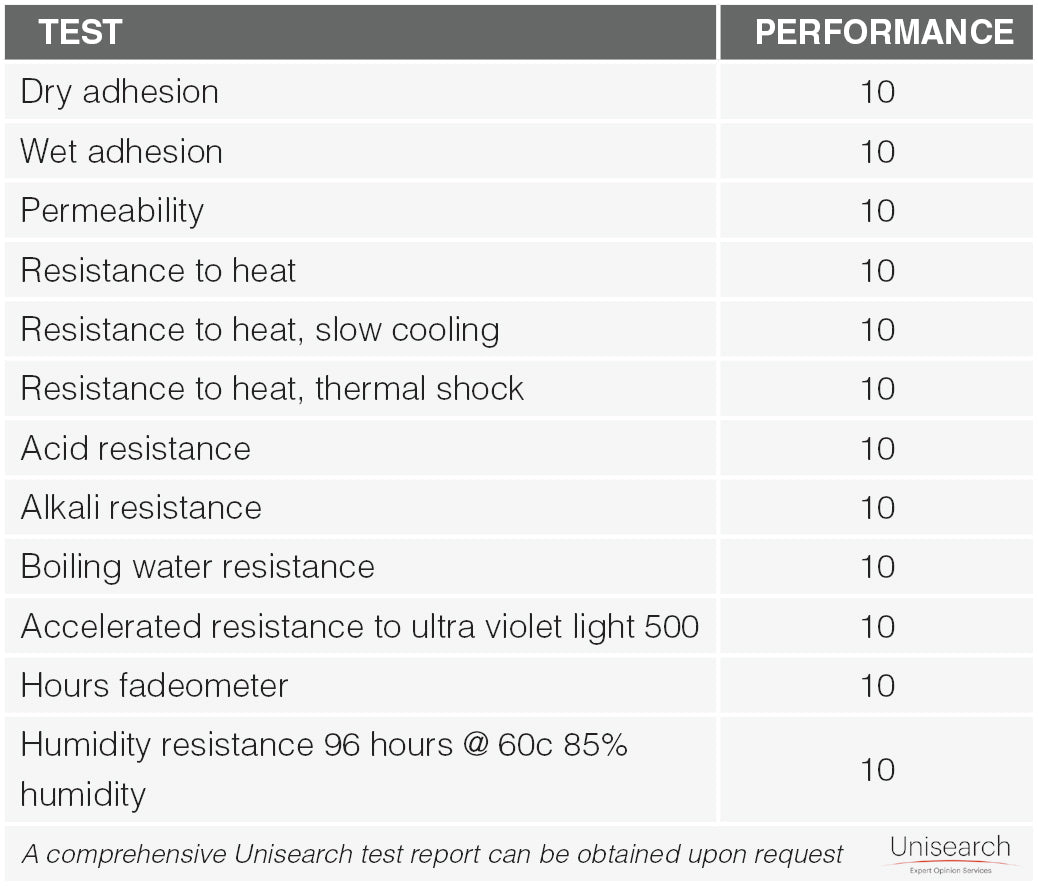